

The reason is that changing the air pressure to achieve pneumatic conveying consumes a large amount of power and is inherently less efficient than a mechanical conveying system’s mechanical transfer. What are the disadvantages of a pneumatic conveying system in comparison to a mechanical conveying system?Ī pneumatic conveying system typically requires far more horsepower to operate than an equivalently sized mechanical conveying system.
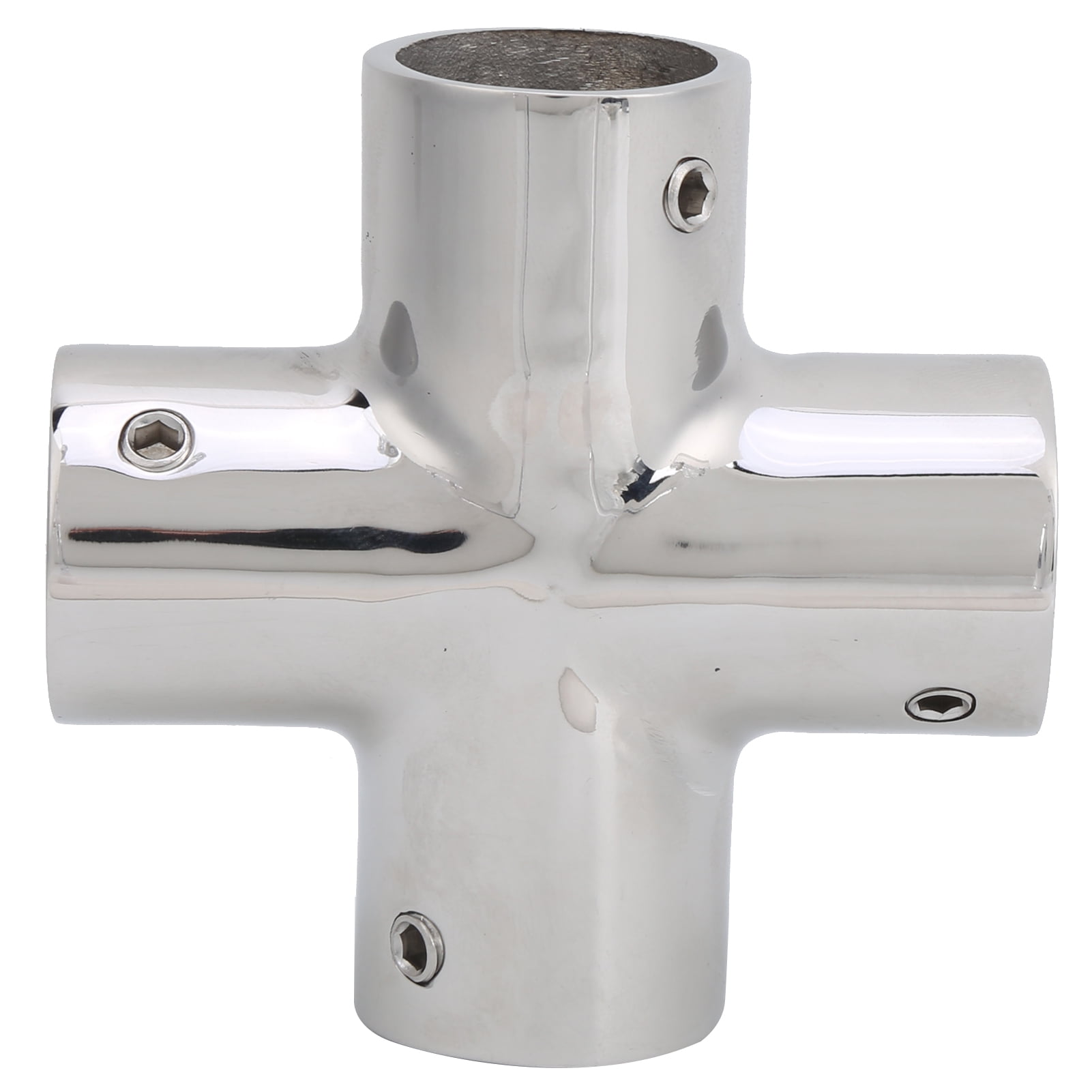

The system is totally enclosed and typically has few moving parts. The pipeline can be arranged with bends to fit around existing equipment, giving the system more layout flexibility, and the system also has a relatively small footprint. On the other hand, a pneumatic conveying system uses a simple, small-diameter pipeline to transfer material. The system also tends to take up a lot of valuable real estate in a plant. It also has a relatively large number of moving parts, which usually require frequent maintenance. The mechanical conveying system may be open rather than enclosed, potentially generating dust. A conventional mechanical conveying system runs in a straight line, with minimal directional changes, and each directional change typically requires its own motor and drive. Let’s start by looking at mechanical conveying systems. What are the advantages of a pneumatic conveying system over a mechanical conveying system? By controlling the pressure or vacuum and airflow inside the system, the system can successfully transfer materials. When located at the system’s end, the air mover pulls air through the system and the system runs under vacuum. Where the air mover is located in the system determines whether it generates one or the other: When located at the system’s start, the air mover pushes air through the system and the system operates under pressure. In a pneumatic conveying system, the air pressure in the conveying line is changed by the system’s air mover, which generates pressure or vacuum. Energy is also required to move material through a pneumatic conveying system, but in this case, the energy is supplied by pressure differential (in pounds per square inch) and airflow (in cubic feet per minute). Such mechanical torque is usually expressed in foot-pounds, and both elements - feet and pounds - are needed to do the work. To turn a bolt, for instance, you need to provide energy in the form of torque. How does a pneumatic conveying system work?ĭoing work requires energy. These materials are usually fairly dry materials in slurry or paste form typically aren’t suited to pneumatic conveying. While some of the most common materials transferred by pneumatic conveying systems are flour, cement, sand, and plastic pellets, any of hundreds of chemicals, food products, and minerals can be pneumatically conveyed. (For simplicity, we’ll call the gas “air” in this article.) The system’s basic elements include a motive air source (also called an air mover, such as a fan or blower), a feeder or similar material-introduction device, a conveying line, a termination vessel (such as an air- material receiver), and a dust collection system. The motive force for this transfer comes from a combination of pressure differential and the flow of a gas, such as air or nitrogen. A pneumatic conveying system transfers powders, granules, and other dry bulk materials through an enclosed pipeline.
